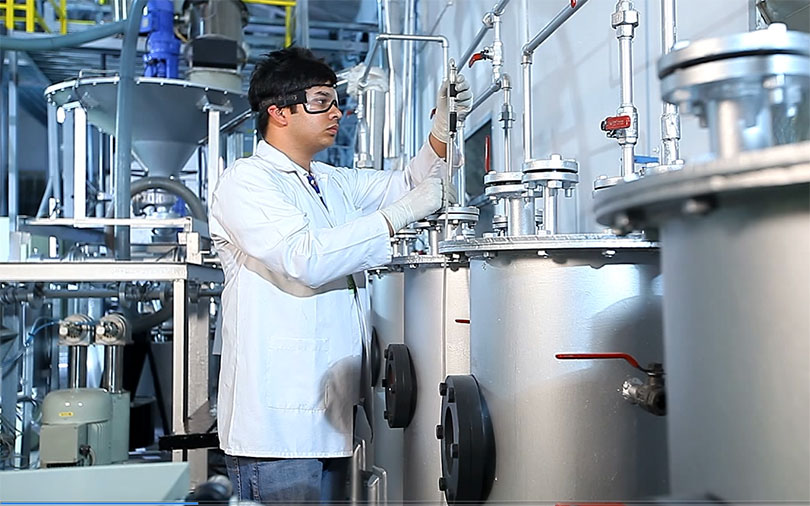
Seven out of every 10 plastic bags head straight for landfills or are simply abandoned somewhere, with heaps of polymer waste across the world having long been identified as a major ecological threat. This dirty, non-recyclable plastic waste suffocates oceans, occupies swathes of land and pollutes the air.
Amit Tandon, a former Silicon Valley engineer, has spent the last seven years in search of a new life for them. In other words, he has been trying to unclog land and water by converting abandoned plastic into a useful new form.
A series of developments in recent months suggest that Tandon is on track to contribute to the global fight against the menace of plastic waste.
His company, PolyCycl Pvt. Ltd, has demonstrated at its plant near Chandigarh that blendstock - material which can be used for making industrial diesel - can be extracted from plastic waste using a cost-effective technology it has developed. Simply put, the company claims it was able to convert plastic into fuel at a lower cost than other companies working on similar technologies.
Last May, US authorities granted Tandon a patent for his extraction technology. Other patents are also in the pipeline.
PolyCycl has since formed a joint venture with waste management company Ramky Group to set up plastic-to-fuel projects in several cities.
The first of such plants that will use the firm’s patented 'Contiflow Cracker' technology is coming up in Hyderabad.
[pull-quote pull_quote_content="PolyCycl received a commitment for a $1.25 million investment from White Field Ventures" pull_quote_alignment="left" /]
In addition, PolyCycl received a commitment for a $1.25 million investment from White Field Ventures - a business group with interests in steel, agriculture and industrial chemicals in the continents of Africa and Europe - as part of an ongoing $5 million funding round in the company.
Sustainable effort
Tandon left Silicon Valley for India after working for a number of startups and Fortune 500 companies including Sun Microsystems.
He was certain about one thing while working on his pet cleantech project - that climate concerns and environmentalism alone will not fuel the recycling of plastic.
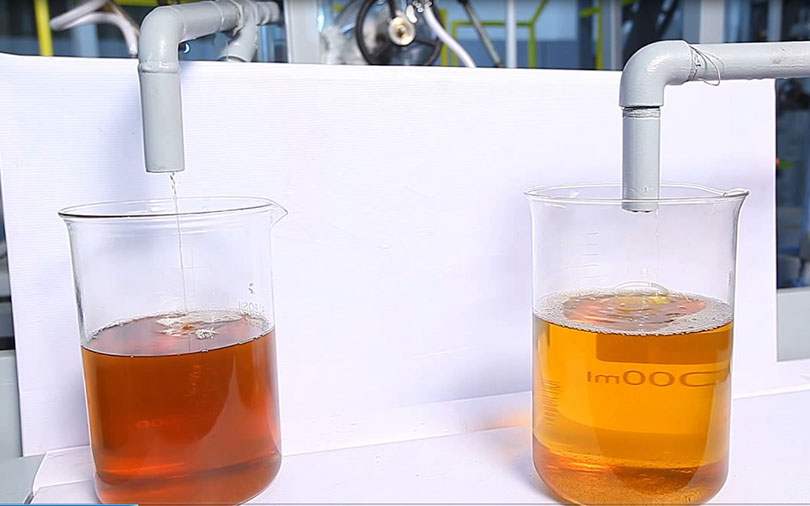
[pull-quote pull_quote_content="“Scalable environmental impact is only possible if there is sound business economics supporting it,” says Tandon." pull_quote_alignment="left" /]
He was convinced he would need to ensure two things in order to make any meaningful impact in redirecting plastics from landfills to crude-extracting recycling plants.
First, the extract should be useful, high-value industrial fuel. Second, the extraction cost should be be kept low.
The existing first generation of plastic-to-fuel systems in the market use a batch-based conversion process, says Dr Ramakrishnan Iyer, vice-president of engineering at PolyCycl.
Not only are such systems operationally cumbersome, they convert waste plastics to a product with lower economic value that is similar to furnace oil.
Tandon claims his firm’s next-generation, fully-continuous depolymerisation process reduces upfront capital cost by 50-75% and operational costs by up to 50%.
“This ensures robust cash flows and that the projects are remuneratively attractive for waste management companies which receive a substantial amount of segregatable waste plastics as part of the material stream they receive every day,” he said.
As opposed to the batch-based systems mentioned earlier, PolyCycl’s technology deploys the company’s patented Contiflow Cracker continuous process for conversion of waste plastics to lighter distillate fuels.
Continuous production implies that the materials being processed are continuously in motion, undergoing chemical reactions or subject to mechanical or heat treatment.
According to PolyCycl, the technology extracts 850 litres of petroleum fuel from one tonne of hydrocarbon-rich plastic waste.
The company says it has sold fuel generated from its demonstration plant to several industrial customers, who in turn use it as blendstock in diesel-fired furnaces and boilers.
The company claims the high price of its diesel blendstock guarantees 50% gross margin.
The road ahead
Gautam Reddy, chief executive officer of Ramky Environment, sees partnering with PolyCycl to convert such low-grade plastic to high-value petroleum fuels as a win-win for both environmental sustainability as well as the economic bottom line.
“Every day we receive several hundred tonnes of non-recyclable waste plastics across our waste management operations in India,” he says.
Even as the engineering work on its Hyderabad plant progresses, PolyCycl has chalked out a business model.
It will license the technology to chemical firms and waste management companies. The other stream of revenue would be joint ventures - akin to the one with Ramky - with several other waste management companies to build and run plastic-to-fuel plants.
“There are already 150 queries from 50 countries,” Iyer claims.
The global efforts towards setting up a new protocol for plastic usage give this startup scope for optimism. The WEF study, ‘The New Plastic Economy', says the linear consumption pattern of the fast-moving consumer goods industry sends goods worth $2.6 trillion to landfills every year.
This calls for a ‘circular economy’, which is essentially the adoption of recycling across the global supply chain.
In addition to investments from White Field Ventures and Ramky Environment, Tandon said, PolyCycl has been shortlisted for investment by a state-run oil and gas company.
PolyCycl received industry body Confederation of Indian Industry’s Indian Innovation Initiative award and showcased its technology at the National Renewable Energy Laboratory Growth Forum in Denver, Clean Energy Forum in Spain, Cleantech Forum in San Francisco and SxSw Eco in Austin.
The aforementioned WEF paper says the plastic innovation engine can move the industry into a positive spiral of value capture, stronger economics and better environmental outcomes. Tandon clearly sees an opportunity to be part of that positive spiral - in his own words, “To do good, while doing good.”